ARMI IN PLASTICA? (PARTE TERZA)
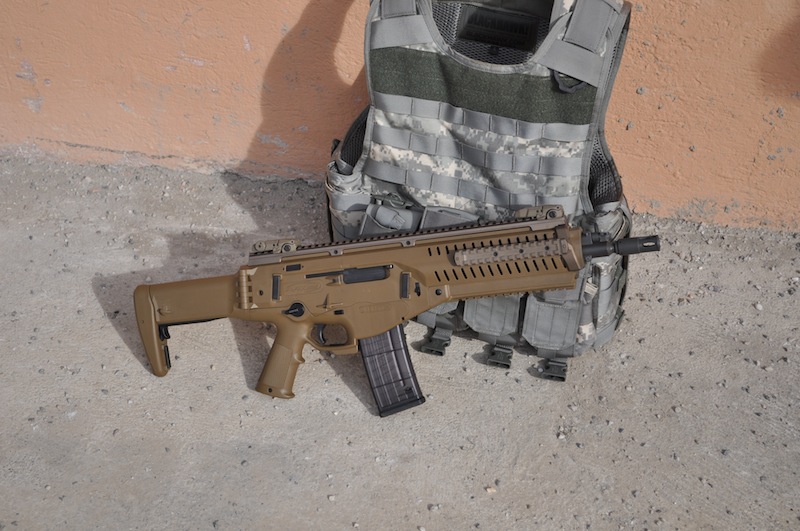
di G.Tansella
Il passo successivo riguarda direttamente il processo di produzione e consiste nella realizzazione degli stampi. Anche in questo caso è necessaria una selezione del materiale da utilizzare poiché alcune materie plastiche, come ad esempio il PVC, sottopongono lo stampo ad uno stress biochimico che ne accelera la corrosione. Tale rischio non è da sottovalutare: lavorare con uno stampo deteriorato comporta gravissime ripercussioni tanto sull’iter produttivo quanto sui suoi costi.
Uno stampo revisionato
La soluzione di questo tipo di problemi comporta la scelta di metalli inossidabili e di opportuni trattamenti di tempratura nella fabbricazione delle matrici. Queste vengono ricavate da blocchi di metallo mediante lavorazioni meccaniche effettuate con l’utilizzo di macchine utensili.
In passato le officine specializzate si avvalevano di esperti meccanici specializzati ma, col passare del tempo, i computer son diventati sempre più diffusi: dei software CAD/CAM (Computer Aided Manufacturing) analizzano il progetto digitale traducendo i dati acquisiti in comandi da impartire a varie macchine utensili computerizzate. Nel caso della AWS queste consistono principalmente in un centro di lavoro CNC ed in macchine a controllo numerico computerizzato per l’elettroerosione a tuffo ed a filo.
Queste due, sfruttando il principio dell’erosione dei metalli per scarica elettrica, realizzano tagli, profili e lavorazioni di straordinaria precisione; il centro di lavoro, vero e proprio robot multifunzione, svolge invece operazioni di taglio, fresatura, asportazione di materiale etc…
Il ruolo delle macchine-utensili classiche conserva tuttavia una grande importanza: gli aggiustamenti e le modifiche vengono in gran parte effettuate in officina per mezzo di, frese, rettificatrici, torni etc…
La parte finale del processo di elaborazione di uno stampo, cioè la lucidatura a specchio delle parti che interagiranno direttamente con la materia plastica, pur potendo l’elettroerosione portare il pezzo alla lappatura, rimane compito dell’uomo: gli operai si servono in questo caso di lucidatrici, meccaniche ed a ultrasuoni, e pasta speciale diamantata.
La matrice realizzata, assolutamente perfetta in ogni singolo dettaglio, verrà poi montata sulle macchine per stampaggio ad iniezione che, tarate “ad hoc”, porteranno a termine la produzione di serie.
Le presse si differenziano principalmente in base alla pressione utilizzata durante il ciclo di funzionamento. Il materiale plastico infatti , potendo assorbire una pressione pari a circa 2000kg per cm2 , viene lavorato in macchine che applicano una pressione complessiva che parte da 15t fino ad arrivare ad oltre 300. Un secondo criterio di distinzione si basa sul peso del singolo pezzo prodotto ad ogni ciclo di stampaggio: i valori vanno da 0,1g a circa 700. Infine le presse si diversificano in base alle prestazioni fornite in termini di volume produttivo all’ora e di lavorazioni effettuate sui pezzi stampati.
Come abbiamo accennato all’inizio la lavorazione del materiale plastico, dalla gomma termoplastica ai polimeri più rigidi, inizia prelevando il semilavorato in granuli per alimentare le singole macchine. Questa operazione può avvenire in modo automatizzato oppure no: le macchine più piccole “aspirano” i granuli di plastica da alcuni recipienti; quelle più grandi si avvalgono dell’ausilio di robot cartesiani che, collegati a speciali sensori, provvedono a rifornirle di continuo (il ciclo operativo può infatti coprire sia la fascia oraria diurna che notturna).
Una volta alimentata la macchina apposite pompe prelevano il granulato a temperatura ambiente e lo convogliano in una camera riscaldata che lo porta alla temperatura di fusione. Ottenuta una sostanza liquida questa viene iniettata nello stampo riscaldato, compressa, raffreddata ed espulsa.
Per ottimizzare i tempi di produzione lo stampo può essere lavorato, a seconda delle dimensioni dei pezzi, per modellarne più di uno nella stessa fase di compressione. La materia plastica raffreddata sarà composta dal pezzo vero e proprio e dai residui della colata, chiamati in gergo “materozze”: alcune macchine sono in grado di dividere i pezzi dagli scarti, altre si limitano a convogliare gli elementi saldati in appositi contenitori lasciando agli operai il compito di separazione. La funzione delle materozze non è, lo ricordiamo, finita: i residui di materiale termoplastico vengono nuovamente ridotti in granuli e andranno in seguito ad alimentare successive fusioni.
Alcuni macchinari sono concepiti per lavorare con apparati accessori che eseguono lavorazioni di finitura: i pezzi, ad esempio, possono subire interventi di impressione a caldo per mostrare scritte e disegni colorati.
Eccoci giunti alla fine dell’iter produttivo degli oggetti in tecnopolimero. La storia della plastica, tuttavia, non finisce qui: alla fine della vita lavorativa, se i pezzi non si saranno biodegradati, verranno recuperati, decomposti e utilizzati per produrre altri manufatti.
Guardando al futuro molti sostengono che le possibilità di sviluppo nel settore della produzione e lavorazione diella materia plastica siano estremamente ampie e, senza peccare di ottimismo, possiamo affermare con certezza che i polimeri rivestiranno ruoli sempre più importanti,. Si parla addirittura di…sostituire l’acciaio: in Germania, patria della lavorazione dei tecnopolimeri, speciali resine termoindurenti vengono utilizzate nella produzione di pistoni pneumatici. Ne parla la rivista “Daily” dell’azienda Arburg, leader nella costruzione di presse per stampaggio ad iniezione. Chi può dire dove arriveremo di questo passo?